The Future of Pneumatic Needle Peening
- Dec 11, 2022
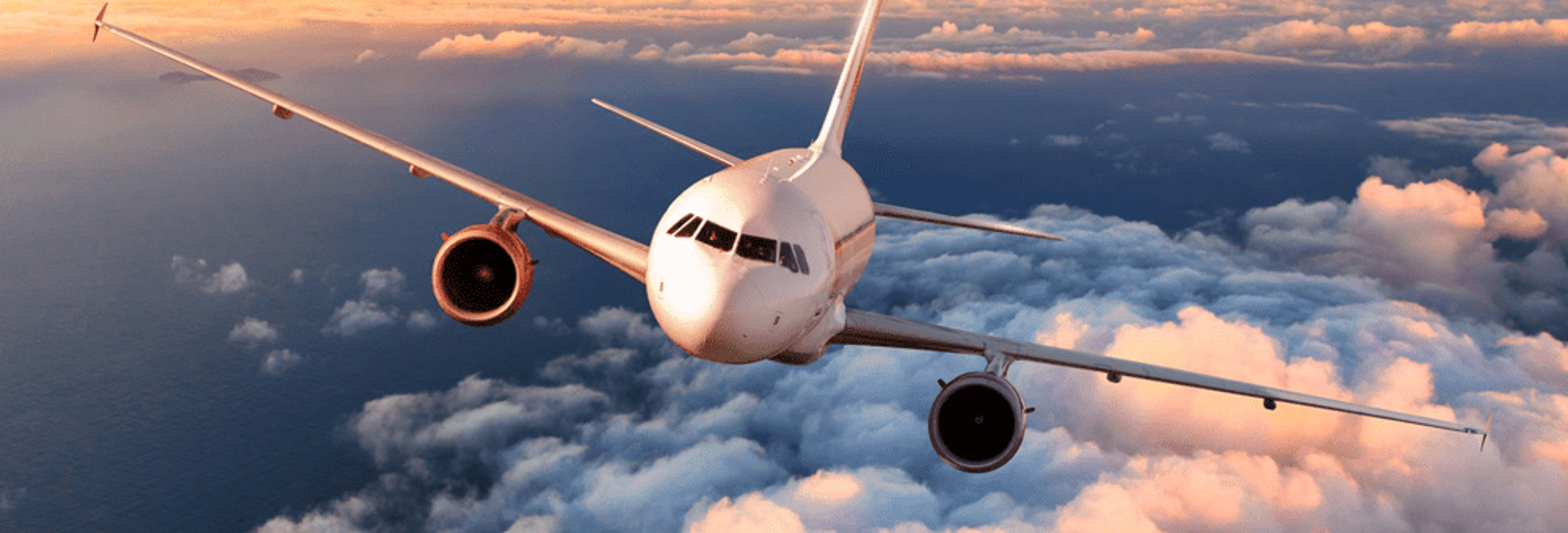
The process of Pneumatic Needle Peening (PNP) is a new emerging technology for the repair and strengthening of aircrafts parts, according to a new whitepaper from the Nadcap© program.
Peening is the hammering of the surface of a metal to induce small deformations that can counteract tensile stress in the material and increase its fatigue life which is critical for things like aircraft parts.
Whitepaper author Mark Hunkele, a Principal Engineer at PRI, the administrator of the Nadcap program, states that PNP offers various improvements over standard shot and flapper peening, including:
- Low risk of foreign object damage to aircraft systems (compared to other peening methods)
- Repairs can be made while the part remains in the vehicle
- Fatigue life of treated parts (including welds) can be substantially improved
- Parts can be treated with minimal masking
- Equipment is portable and can be used in tight applications
- Significant improvement in surface roughness over conventional peening
Applications for the needle peening process in the aerospace industry include landing gear assemblies, wing spars, and helicopter rotor hubs. The paper notes that it is also being used in the nuclear industry for treating coolant pump assemblies, primary loop piping, and steam generator tubing. It is also used to peen along welds to add compressive stress back into the surface layer of the weld which can significantly increase the life of the weld.
One of the reasons for the practicality of PNP, according to the whitepaper, is its portability. Several companies currently supply portable PNP, including Shockform Aeronautics’ Spiker® system, and SONATS’ Stressvoyager® product. Given that this is an emerging technology, additional applications and products may be announced.
The whitepaper notes that the only shortcoming to PNP is that its coverage rate falls short of the coverage capability of conventional shot peening. The author adds, however, that as a new technology, PNP “provides a strong method for peening in the aerospace industry into the future.”
A Nadcap accreditation process in PNP is being developed, and one already exists for conventional flapper peening. Achieving a Nadcap accreditation can enable a supplier to demonstrate their ability to meet established standards set by the OEM aerospace companies that are Subscribers to the Nadcap program.
Nadcap Audit Checklists for both the PNP and conventional flapper peening processes are also currently available. Audit checklists are used to help a company prepare for a Nadcap accreditation audit covering a specific process.
To read or download the new Nadcap whitepaper on Pneumatic Needle Peening, visit the Resources section of the PRI website: https://p-r-i.org/resources/listing/?lang=&p19=nadcap&c32=whitepapers.
If you’d like additional information about Nadcap, email Nadcapinfo@p-r-i.org.